Entwicklung eines Mehrkomponenten-Spritzgießprozesses zur Herstellung von medizintechnischen Multifunktionsteilen aus Standardthermoplasten und Silikonkautschuken (MeKoMed)
Stellen Sie sich Ihre individuelle Projektübersicht zusammen.
Schlagwort: Medizintechnik
Fördermaßnahme: Produktion für Medizintechnik - wirtschaftlich und in höchster Qualität (ProMed)
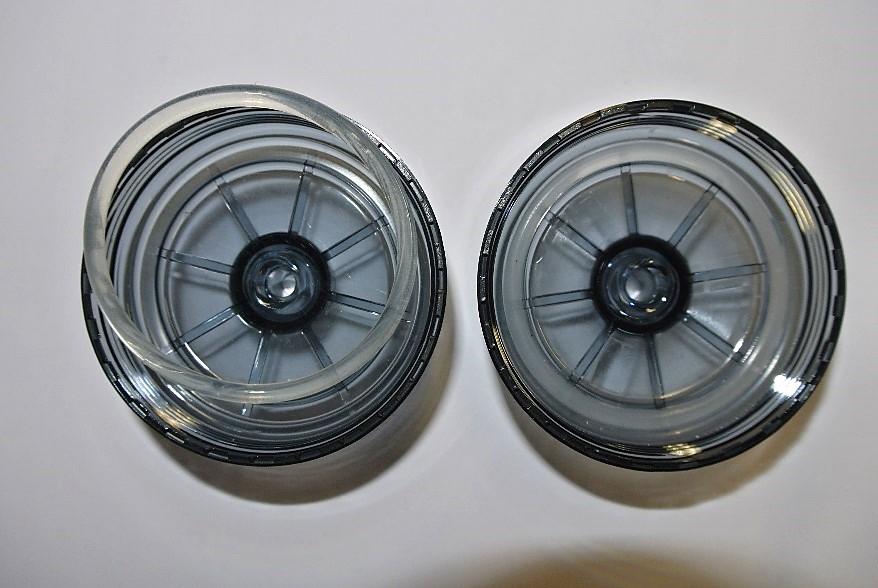
Forschungsziel: Das Forschungsvorhaben MeKoMed zielte auf eine integrierte Produktionstechnologie, mit der erstmalig Multifunktionsbauteile aus Standard-Thermoplast und Silikonelastomer im Mehrkomponentenspritzguss für Medizintechnik direkt gefertigt werden können. Vorhabensziel war die Erforschung der Prozesstechnologie zur integrierten Verarbeitung der zwei Materialklassen mit sehr unterschiedlichen Bearbeitungsfenstern. Ebenfalls sollte die erforderliche Werkzeugtechnik entwickelt werden, wobei der Fokus auf einer hochdynamischen Temperierung und auf einer intelligent geregelten Heißkanaltechnik lag.
Ansprechperson Projektkoordination
Dieter Göppert +49 7821 9503-12
d.goeppert@polar-form.de
Ansprechperson bei PTKA
Dipl.-Ing. Claudius Noll
+49 721 608-24953
claudius.noll@kit.edu
Problemstellung
Silikonelastomere eignen sich aufgrund ihres besonderen Eigenschaftsprofils sehr gut für den Einsatz in der Medizintechnik. Als Funktionselemente (Dichtungen, Membranen oder Ventile) in medizinischen Komponenten werden diese nach Stand der Technik über Füge- und Montageprozesse in thermoplastische Gehäuse (Standard-Thermoplaste wie ABS, PE, PP oder PS) integriert. Eine Substitution durch einen Mehrkomponentenspritzgießprozess, der eine wirtschaftlichere, höher automatisierte und qualitativ hochwertigere Produktion ermöglichen würde, ist aktuell technisch nicht realisierbar. Durch die bisher erforderlichen Füge- und Montageschritte ist die Produktion von Multifunktionsbauteilen aus thermoplastischem Gehäuse mit silikonbasierten Funktionselementen gegenwärtig zeit- und kostenaufwändig. Zugleich erschwert die mehrstufige Prozesskette eine Gewährleistung von Hygiene- und Prozesssicherheit.
Ziel
Das Forschungsvorhaben MeKoMed zielte auf eine integrierte Produktionstechnologie, mit der erstmalig Multifunktionsbauteile aus Standard-Thermoplast und Silikonelastomer im Mehrkomponentenspritzguss direkt gefertigt werden können. Vorhabensziel war die Erforschung der Prozesstechnologie zur integrierten Verarbeitung der zwei Materialklassen mit sehr unterschiedlichen Bearbeitungsfenstern. Ebenfalls sollte die erforderliche Werkzeugtechnik entwickelt werden, wobei der Fokus auf einer hochdynamischen Temperierung und auf einer intelligent geregelten Heißkanaltechnik lag.
Vorgehensweise
Als Grundlage wurde zunächst das differenzierte Anforderungsprofil an Prozess und Anlagentechnik entsprechend der regulatorischen Vorgaben und Anwendungsanforderungen in der Medizintechnik analysiert. Darauf aufbauend wurde der Prozess erforscht, wobei sowohl experimentelle Arbeiten als auch modellbasierte Simulationen eingesetzt wurden, um die optimale Führung von Parametern wie Druck und Temperatur systematisch zu erarbeiten. In Abstimmung mit dem Prozess wurde die erforderliche Werkzeugtechnik entwickelt. Hierbei lag der Fokus auf der hochdynamischen Temperierbarkeit des Werkzeugs (steile Heiz- und Kühlrampen), die durch elektrische/induktive Beheizung und geeigneten Werkstoffeinsatz sowie entsprechende Konstruktion des Werkzeugs umgesetzt wurde. Ebenfalls wurde eine spezielle Heißkanaltechnik einschließlich einer sensorbasierten Regelung entwickelt, wodurch weitere Möglichkeiten zur komplexen und zugleich stabilen Prozessführung erschlossen wurden.
Ergebnisse und Anwendungspotenzial
Die Umsetzung im Projekt wurde unter Berücksichtigung technischer und regulatorischer Anforderungen der Medizintechnik dahingehend gestaltet, dass eine Übertragung auf eine hohe Anzahl von aktuellen und zukünftigen Produkten möglich ist. Über eine Validierung des Produktionsprozesses wurde ein Nachweis zur reproduzierbaren Qualität der Fertigung erbracht. Durch eine flankierende Erforschung der Auslegungssystematik und thermisch kompatibler Werkzeugeinsätze wurde ein Gesamtergebnis angestrebt, dass von der fertigungsoptimalen Produktauslegung bis zur wirtschaftlichen Produktion reichte und damit eine ebenso zukunftssichere wie anwendungsrelevante Lösung realisierte. Damit wurden neue Möglichkeiten in der Konzeption und Produktion funktionaler Bauteile eröffnet. Eine gesteigerte Bauteilqualität führte zur Erhöhung der Patientensicherheit. Zugleich ermöglichte die hygienesichere, montagefreie Produktion als dokumentationsfähige, validierte Gesamtlösung eine auch für KMU vereinfachte Entwicklung und Produktion von Medizintechnikprodukten. Durch den Ergebnistransfer über Fachbeiträge (Publikationen, Vorträge), Diskussionen mit Branchenexperten, sowie Einbringung in Forschung und Lehre/berufliche Bildung in der Kunststofftechnik kamen die Ergebnisse auch einem breiten Kreis potenzieller Anwender zugute und wurden als Grundlage für weitere FuE in Deutschland etabliert.
- B. Braun Melsungen Aktiengesellschaft
- EWIKON Heißkanalsysteme GmbH
- Freudenberg Medical Europe GmbH
- M + S Silicon Formteile GmbH
- POLAR-FORM Werkzeugbau GmbH
- Universität Kassel
Ihre Favoriten
In der folgenden Liste sehen Sie Ihre ausgewählten Projekt-Favoriten.