Funkenerosive (EDM) und elektrochemische (ECM) Hochleistungsendbearbeitung von feingegossenen und generativ hergestellten Turbolader-Turbinenrädern aus Gamma-Titanaluminid für den Automobilbau (ETurbo)
Stellen Sie sich Ihre individuelle Projektübersicht zusammen.
Fördermaßnahme: Hochleistungsfertigungsverfahren für die Produkte von Morgen - Technologieinnovationen auf dem Weg zur intelligenten Fertigung
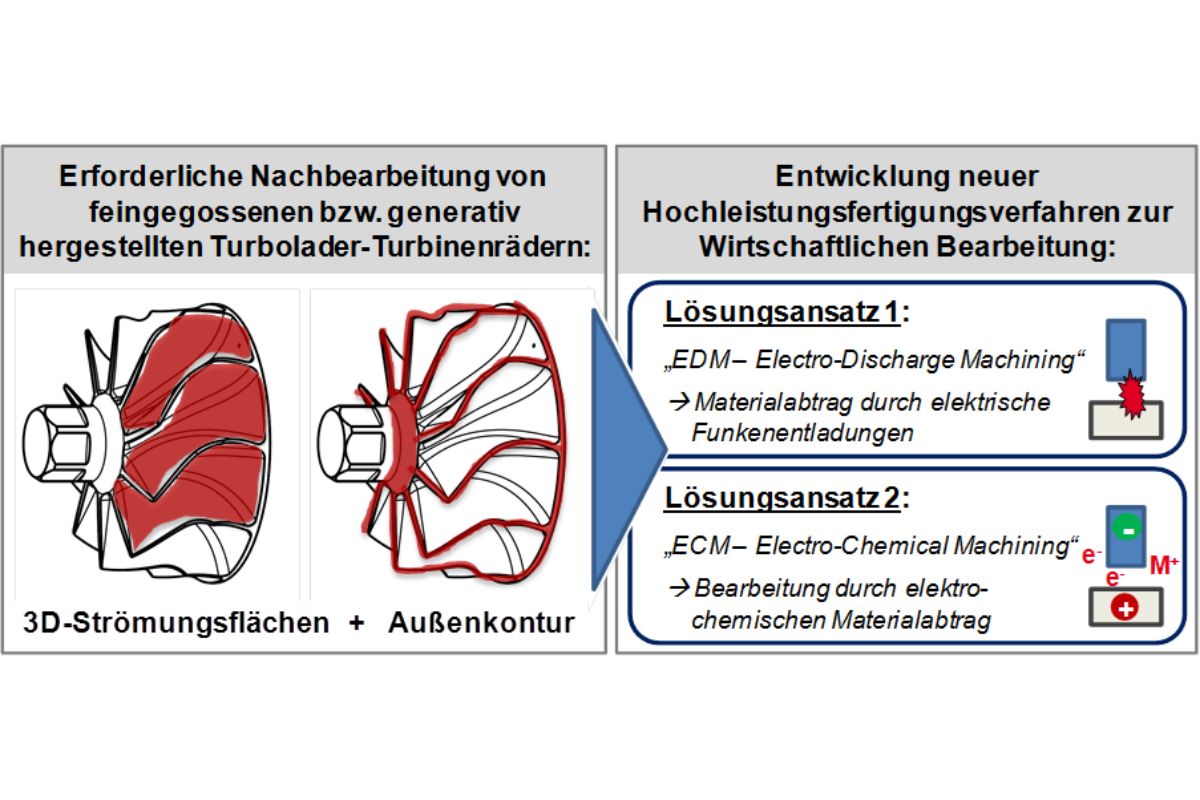
Forschungsziel: Bei modernen Verbrennungsmotoren im Fahrzeugbau werden mit Turboladern erhebliche Leistungssteigerungen erreicht. Dies führt dazu, dass die Motoren bei gleicher Leistung sehr viel kleiner dimensioniert werden können. Um die Leistungsausbeute weiter zu steigern, müssen Turboladersysteme entwickelt werden, die mit immer höheren Abgastemperaturen betrieben werden können. Neuartige Werkstoffe auf Basis von Gamma-Titanaluminid (TiAl) erfüllen die hierfür geforderten Anforderungen an Hochtemperatureignung und Leichtbau. Ziel ist es, funkenerosive und elektrochemische Hochleistungsfertigungsprozesse zu entwickeln, bei dem der Werkstoff thermisch durch einen Funken, der zwischen der Werkzeugelektrode und dem Werkstück überschlägt, punktförmig abgeschmolzen oder verdampft wird.
Ansprechperson Projektkoordination
Dr. Marcus Hlavac +49 711 811-33689
marcus.hlavac@de.bosch.com
Ansprechperson bei PTKA
Dipl.-Ing. Mischa Leistner
+49 721 608-31429
mischa.leistner@kit.edu
Problemstellung:
Bei modernen Verbrennungsmotoren im Fahrzeugbau werden mit Turboladern erhebliche Leistungssteigerungen erreicht. Dies führt dazu, dass die Motoren bei gleicher Leistung sehr viel kleiner dimensioniert werden können. Hinzu kommt, dass diese Motoren weniger Kraftstoff verbrauchen und damit weniger Emissionen verursachen. Um die Leistungsausbeute weiter zu steigern, müssen Turboladersysteme entwickelt werden, die mit immer höheren Abgastemperaturen betrieben werden können. Neuartige Werkstoffe auf Basis von Gamma-Titanaluminid (TiAl) erfüllen die hierfür geforderten Anforderungen an Hochtemperatureignung und Leichtbau. Aufgrund der schwer zugänglichen und zugleich filigranen 3D-Strömungsgeometrien sowie den speziellen Werkstoffeigenschaften von Gamma-Titanaluminden, wie Sprödheit und schwerer Zerspanbarkeit, stellt die Endbearbeitung von Turbolader-Turbinenrädern eine große technologische Herausforderung dar, die mit bestehenden zer-spanenden Fertigungsverfahren nicht wirtschaftlich gelöst werden kann.
Projektziele:
Ziel des Forschungsprojekts ETurbo ist die Entwicklung eines funkenerosiven und elektrochemischen Hochleistungsfertigungsverfahrens, bei dem der Werkstoff thermisch durch einen Funken, der zwischen der Werkzeugelektrode und dem Werkstück überschlägt, punktförmig abgeschmolzen oder verdampft wird. Das Werkstück wird dabei mechanisch nicht belastet und die Werkstückbearbeitung ist unabhängig von der Materialhärte der Gamma-Titanaluminde möglich. Das neuartige Verfahren soll sich durch eine gesteigerte Leistungsfähigkeit gegenüber den praktizierten spanenden Fertigungsverfahren auszeichnen.
Vorgehensweise:
Für die funktionsrelevante komplexe 3D-Strömungsgeometrie der Turbinenräder steht die Kombination und die Entwicklung von funkenerosiven und elektrochemischen Wirkprinzipien im Fokus, die eine Komplettbearbeitung der Turbinenschaufeln in einem Prozessschritt ermöglichen. Für die effiziente Bearbeitung der Außenkontur sollen am Projektende mit Drahtelektroden arbeitende Abtragverfahren zur Verfügung stehen, die eine parallele Endbearbeitung von mehreren Turbolader-Turbinenrädern gestatten. Die angestrebte Steigerung der Produktivität, Wirtschaftlichkeit sowie der Ressourceneffizienz verbunden mit gleichzeitiger Verringerung der Umweltbelastung werden dabei in einem konkreten Technologiebenchmark für die Fertigung eines Gamma-TiAl Turbolader-Turbinenrades aufgezeigt.
Ergebnisverwertung:
Bei erfolgreicher Umsetzung der Projektidee können PKW-Turbolader aus TiAl-Legierungen hergestellt werden, die mit sehr hohen Abgastemperaturen betrieben werden können. Damit werden Kraftstoffverbrauch und Emissionen der Verbrennungsmotoren deutlich reduziert. Diese Fertigungsverfahren können auch für die Bearbeitung von unterschiedlichsten Komponenten aus schwer zerspanbaren Werkstoffen einsetzbar sein, wie z. B. Funktionsbauteile aus dem Bereich der Energie- und Anlagentechnik sowie der Luft- und Raumfahrttechnik.
- ACCESS e.V.
- EMAG ECM GmbH
- OPS-INGERSOLL Funkenerosion GmbH
- Robert Bosch GmbH
- RWTH Aachen
- VWH GmbH
Ihre Favoriten
In der folgenden Liste sehen Sie Ihre ausgewählten Projekt-Favoriten.