Innovative Prozesskette zur Massivteilfertigung aus einem neuartigen Leichtbaustahl (IPROM)
Stellen Sie sich Ihre individuelle Projektübersicht zusammen.
Schlagwort: Industrie 4.0
Fördermaßnahme: Hochleistungsfertigungsverfahren für die Produkte von Morgen - Technologieinnovationen auf dem Weg zur intelligenten Fertigung
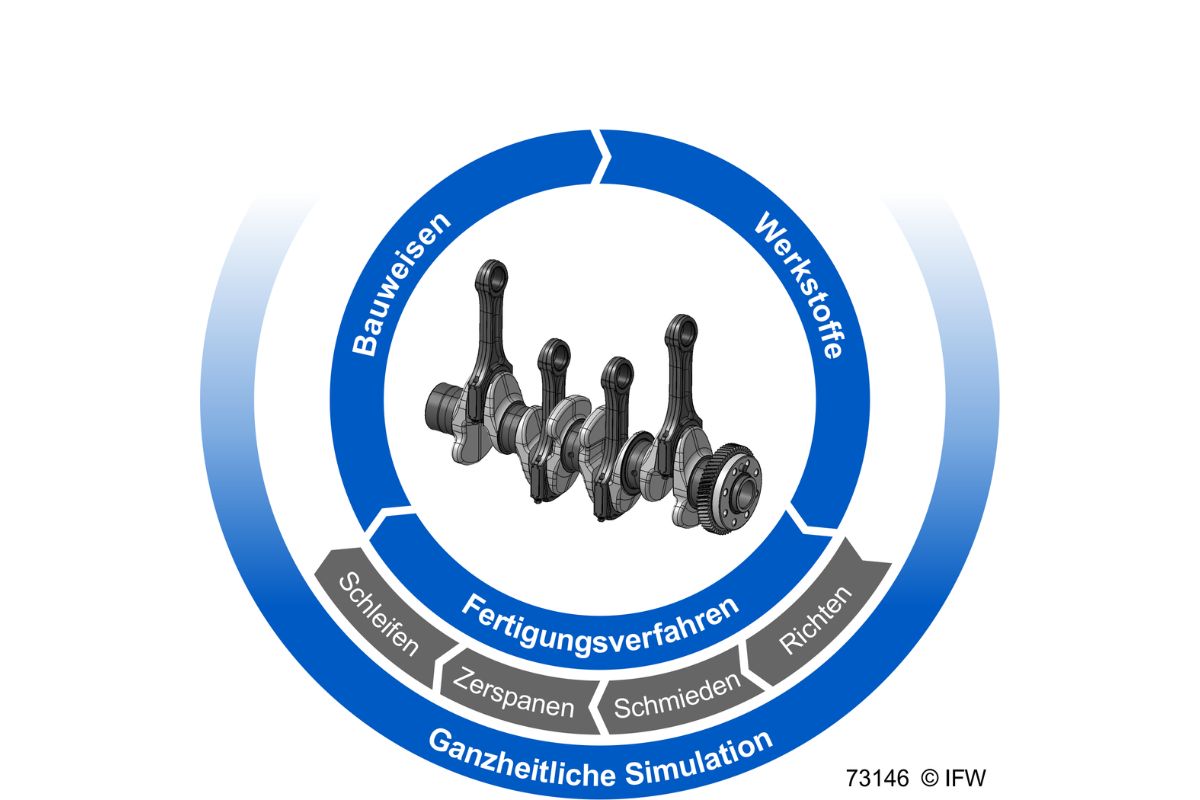
Forschungsziel: Im Mittelpunkt des Verbundvorhabens IPROM steht die Entwicklung und Bereitstellung von Hochleistungsfertigungstechnologien (Umformen, Spanen, Schleifen) für eine wirtschaftliche und prozesssichere Herstellung von Massivbauteilen aus einem aluminiumlegierten Leichtbaustahl. Am Ende des Vorhabens soll an zwei typischen Bauteilen aus einem Verbrennungsmotor nachgewiesen werden, dass es möglich ist, diese Bauteile sicher herzustellen und damit die Voraussetzungen zu schaffen, das Leichtbaupotential des Materials auszunutzen.
Ansprechperson Projektkoordination
Ansprechperson bei PTKA
Dipl.-Ing. Michael Petzold
+49 721 608-31469
michael.petzold@kit.edu
Problemstellung
Aluminiumlegierte Leichtbaustähle verfügen im Vergleich zu heutigen Hochleistungsstählen über vergleichbare Festigkeiten bei einer um ca. 10% reduzierten Dichte. Aufgrund der hervorragenden Rohstoffverfügbarkeit und den zu niedriglegierten Stählen vergleichbaren Herstellungskosten besitzen diese Leichtbaustähle das Potenzial, andere Stahlsorten in bestimmten Anwendungsfeldern zu substituieren. Bisherige Untersuchungen haben ergeben, dass die mechanischen und thermischen Eigenschaften aluminiumhaltiger Leichtbaustähle zu äußerst anspruchsvollen Prozessbedingungen in der Fertigung führen. Trotz umfangreicher Vorarbeiten konnte bislang kein Durchbruch bei der trennenden und umformenden Bearbeitung von Leichtbaustählen erzielt werden. Ein potentieller industrieller Einsatz dieser vielversprechenden Werkstofffamilie bedarf eines intensiveren Verständnisses der fertigungstechnischen Zusammenhänge für ein produktives Umfeld sowie einer ressourceneffizienten Prozesskette. Dies kann nur dadurch erfolgen, indem künftig neuartige Hochleistungsfertigungsverfahren für derart anspruchsvolle, zukunftsweisende Werkstofffamilien bereitgestellt werden.
Projektziele
Hauptziel des Forschungsvorhabens ist die Entwicklung und Verfügbarkeit von Hochleistungsfertigungstechnologien für eine wirtschaftliche und prozesssichere Herstellung von Massivbauteilen am Beispiel der Herstellungskette eines aluminiumlegierten Leichtbaustahls. Die Herstellung und/oder Legierungsoptimierung des ausgewählten Leichtbaustahls ist hierbei nicht Gegenstand der Untersuchungen.
Vorgehensweise
Die beteiligten Projektpartner verfolgen das Ziel, maßgeschneiderte umformende und trennende Hochleistungsfertigungsverfahren zu entwickeln, so dass eine großflächige serientechnische Anwendung dieser oder vergleichbarer Werkstofffamilien am Industriestandort Deutschland künftig branchenübergreifend möglich ist. Im Einzelnen plant die Deutsche Edelstahlwerke GmbH in Zusammenarbeit mit dem Institut für Umformtechnik und Umformmaschinen (IFUM) der Leibniz Universität Hannover die Entwicklung innovativer Richt- und Trennverfahren (Scheren, Hochgeschwindigkeitstrennen und -sägen) zur Halbzeugherstellung (Stabmaterial). Moderne Prüfverfahren wie die Ultraschallprüfung werden auf die Erfordernisse aluminiumhaltiger Leichtbaustähle angepasst. Im Hinblick auf eine Prozesskettenverkürzung und zur Erhöhung der Ressourceneffizienz erprobt die Daimler AG als Konsortialführer in Zusammenarbeit mit dem IFUM das Fließpressen von Kolbenbolzen und Gesenkschmieden von Pleuel. Die Partner Walter AG, Mapal KG und das Institut für Fertigungstechnik und Werkzeugmaschinen (IFW) der Leibniz Universität Hannover werden im Bereich der Zerspanung mit geometrisch bestimmter Schneide ihre Expertise speziell in den Bereichen der Kühlschmierstoffstrategien und -zuführung (Kühlkanaldesign) sowie in der Entwicklung von Werkzeugkonzepten einbringen, die im Hinblick auf Beschichtung und Schneidkantenmikrogeometrien auf die neuartige Werkstofffamilie angepasst sind. Die Entwicklung von Lasersintertechnologien für die Werkzeugherstellung durch die Mapal KG zielt auf die beschleunigte Entwicklung neuer Sonderwerkzeuge ab. Die Hermes Schleifkörper GmbH erarbeitet in Zusammenarbeit mit dem IFW hochporöse Schleifscheibenkonzepte auf der Basis von Agglomeraten. Die Herausforderung, unterschiedliche Fertigungsprozesse zugleich für einen neuen Werkstoff zu entwickeln, wird als Chance begriffen die aluminiumhaltigen Leichtbaustähle umfassend zu modellieren. Die zwischen Materialkunde, Umform- und Zerspanungstechnik entstehenden Synergien werden durch diesen Ansatz optimal genutzt. Durch eine ganzheitliche, simulationsgestützte Prozesskettenoptimierung werden die Wechselwirkungen zwischen den Prozesskettenelementen berücksichtigt. Die erarbeiteten grundlegenden Erkenntnisse werden kontinuierlich durch die Projektpartner in eine prototypische Prozesskette zur Herstellung von Massivbauteilen (Pleuel, Kolbenbolzen) übertragen und an weiteren schwer fertigbaren Werkstoffen vergleichsweise validiert.
Ergebnisverwertung
Die entwickelten Hochleistungsfertigungsverfahren am Beispiel der Leichtbaustahlfamilie lassen sich über die pilothafte Anwendung der Pleuel- oder Kolbenbolzenherstellung hinaus auf andere Bauteile in der Schifffahrts-, Druck- oder Agrarindustrie übertragen. Die Werkzeug- und Kühlkonzepte für die Zerspanung können synergetisch von der Mapal KG, der Hermes GmbH und der Walter AG auch auf andere schwer zerspanbare Werkstoffe übertragen werden. Insgesamt besitzt das Vorhaben über die beteiligten Projektpartner hinaus außerordentliche Bedeutung für den Hochtechnologiestandort Deutschland.
- Deutsche Edelstahlwerke Specialty Steel GmbH & Co. KG
- Hermes Schleifmittel GmbH
- Leibniz Universität Hannover
- MAPAL Fabrik für Präzisionswerkzeuge Dr. Kress K.-G.
- Mercedes-Benz AG
- WALTER Aktiengesellschaft
Ihre Favoriten
In der folgenden Liste sehen Sie Ihre ausgewählten Projekt-Favoriten.