Prozess- und Systemtechnik zur Hybrid-Fertigung großer Bauteile mit dem Laser Metal Deposition (LMD) Verfahren (ProLMD)
Stellen Sie sich Ihre individuelle Projektübersicht zusammen.
Fördermaßnahme: Additive Fertigung - Individualisierte Produkte, komplexe Massenprodukte, innovative Materialien (ProMat_3D)
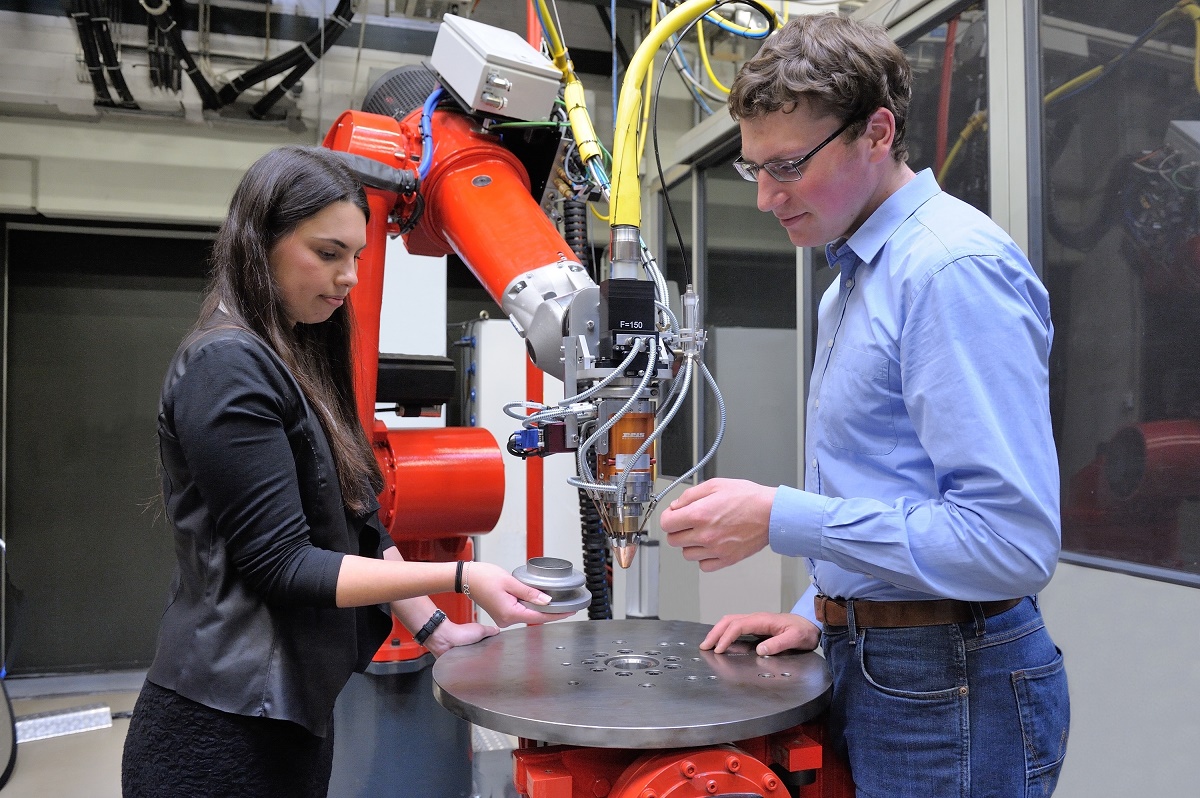
Forschungsziel: Ziel des Forschungsprojekts ProLMD war die Entwicklung eines wirtschaftlichen Herstellungsverfahrens zur hybriden Fertigung von großen Hochleistungsbauteilen. Die entwickelte Systemtechnik und die erweiterten LA-Prozesse wurden an Demonstrator-Bauteilen der beteiligen Industriepartner demonstriert. Es wird erwartet, dass bei erfolgreicher Umsetzung nach Ende des Projektes über 10 Prozent der Kosten für die gesamte Prozesskette eingespart werden können. Die erhebliche Ressourcenschonung und die erhöhte Freiheit in der Produktentwicklung machen die Ergebnisse auch für weitere Branchen, wie Raumfahrt, Energieerzeugung und den durch KMU geprägten Werkzeugbau, wirtschaftlich und technologisch interessant.
Ansprechperson Projektkoordination
Günter Neumann +49 2405 45468-10
g.neumann@kuka.com
Ansprechperson bei PTKA
Dipl.-Ing. Stefan Scherr
+49 721 608-25286
stefan.scherr@kit.edu
Problemstellung
Bei der Fertigung von Hochleistungs- und Leichtbauteilen, wie im Flugzeugbau, werden heutzutage bis zu 90 Prozent des Rohmaterials abgetragen und müssen wieder aufbereitet werden. Die sogenannte hybride Fertigung stellt eine Alternative zu diesen abtragenden Verfahren dar. Sie nutzt konventionell hergestellte Rohteile, auf denen zusätzliche Geometrieelemente additiv durch Laserauftragschweißen (LA) aufgebracht werden. Zudem müssen empfindliche Materialien beim LA durch Schutzgas vor Oxidation geschützt werden. Der bisherige Ansatz, die ganze Anlage unter Schutzgasatmosphäre zu bringen, begrenzt die Bauteilgröße und ist kostenintensiv.
Projektziel
Ziel des Forschungsprojekts ProLMD war die Entwicklung eines wirtschaftlichen Herstellungsverfahrens zur hybriden Fertigung von großen Hochleistungsbauteilen. Die entwickelte Systemtechnik und die erweiterten LA-Prozesse wurden an Demonstrator-Bauteilen der beteiligen Industriepartner demonstriert.
Vorgehensweise
Hierbei wurde eine neue Systemtechnik auf Basis von Industrierobotern entwickelt. Dies senkt Kosten und steigert die Flexibilität hinsichtlich Bauteilgeometrie und -größe. Ein flexibles Schutzgassystem wurde erarbeitet, welches nur dort Schutzgas verwendet, wo es nötig ist. Neue Laserbearbeitungsköpfe, die sowohl mit Draht als auch mit Pulver als Zusatzwerkstoff arbeiten, sowie eine für die hybride Fertigung geeignete Software runden die Systementwicklung ab. Parallel wurden für mehrere Werkstoffe, sowohl in Draht- wie auch Pulverform, Laserauftrag-Prozesse erforscht. Als Basis für eine Verwendung in hochbelasteten Bauteilen wurden ausführliche Materialuntersuchungen durchgeführt und eine geometrische Überprüfung der aufgebauten Bauteile mittels einer angepassten Messtechnik implementiert. Die Prozesskette wurde erfolgreich an Anwendungen der Projektpartner am Beispiel von Triebwerksgehäusen, einer Bauteilverstärkung durch 3D-Verrippung und der Anpassung eines Presswerkzeugs in der Karosseriefertigung demonstriert.
Ergebnisse und Anwendungspotenzial
Es wird erwartet, dass bei erfolgreicher Umsetzung nach Beendigung des Projektes über 10 Prozent der Kosten für die gesamte Prozesskette eingespart werden können. Die erhebliche Ressourcenschonung und die erhöhte Freiheit in der Produktentwicklung machen die Ergebnisse auch für weitere Branchen, wie Raumfahrt, Energieerzeugung und den durch KMU geprägten Werkzeugbau, wirtschaftlich und technologisch interessant.
- Airbus Defence and Space GmbH
- BCT Steuerungs- und DV-Systeme GmbH
- Fraunhofer-Gesellschaft zur Förderung der angewandten Forschung eingetragener Verein
- Laserline Gesellschaft für Entwicklung und Vertrieb von Diodenlasern mbH
- M. Braun Inertgas-Systeme GmbH
- Mercedes-Benz AG
- MTU Aero Engines AG
- Reis Robotics GmbH & Co. KG
Ihre Favoriten
In der folgenden Liste sehen Sie Ihre ausgewählten Projekt-Favoriten.